CNC G-Code Simulator
ICAM’s Virtual Machine®
Detect & Eliminate Collisions, Surface Gouges & More with a High-Precision CNC Simulator
Compared to traditional APT-based simulation systems, which only simulate the planned tool-path, ICAM’s Virtual Machine® delivers for a more meaningful simulation, accurately recreating how the machine tool will react to the G-code generated by your post-processor.
The simulator provides a powerful validation method allowing users to determine the association between G-code and specific operations inside the NC program and allows for specific modifications to the CAD/CAM NC program depending on the simulation results.
Supports a Wide Range of CAD/CAM Systems
Virtual Machine® is built for complete compatibility with all major CAD/CAM systems like CATIA, NX CAM, creo & Mastercam. This flexibility allows the software to be quickly and easily integrated into your existing workflow with minimal implementation time.
Don’t see you’re software listed? Click here to see the complete list.
Compatible with All Types & Models of CNC Machines & Controllers
Virtual Machine’s advanced simulation capabilities support all major makes and models of CNC Machine-Controller pairings including industry leaders like Mazak, Fanuc & Siemens.
Don’t see you’re brand listed? Click here to see the complete list of our supported machines & controllers.
Cutting-Edge Features to Meet the Biggest Machining Challenges
ICAM’s Virtual Machine® has helped countless manufacturers gain a competitive edge by reducing costly CNC machine collisions and repetitive shop-floor proofing of parts through its advanced set of features.
Supports Mill/Turn Machining Centers
Virtual Machine® features full support for mill/turn centers including synchronizing dual turret merging lathes, accurately simulating constant surface speed as well as defining and modeling lathe tool inserts and generic 3D tool holders. Virtual Machine® also provides the environment to define a rotary axis as either a spindle or a lathe tool turret providing greater support for different machines.
Multi-Setup
This feature supports Virtual Machine® simulation of manufacturing processes that involve one or more changes of clamping and/or part location on the machine. Multi-setup also automatically tracks the in-process stock state as a part progresses from one manufacturing program to another.
Simulation Recording
This feature automatically records the complete post-processing and simulation session for later review and analysis. Programs can be post-processed with Virtual Machine® simulation overnight and/or in the background and then later viewed on the same or a different workstation.
Material Removal
Virtual Machine® supports superior material removal capabilities for in-process stock collision and gouge detection. This functionality allows NC programmers to compare the processed stock model to the original CAD/CAM design. Virtual Machine® computes in-process stock geometry to identify and display gouges, excess material, inaccessible areas and rapid-motion collisions during the post-processing and verification phase.
Unique Timeline Control
Virtual Machine® offers a unique Timeline Control that provides bi-directional review and playback of NC programs at any moment within the machining cycle. This unique function allows programmers to visualize and test NC post-processor for maximum output optimization.
Cost-Effective NC Tape Proofing
Virtual Machine® detects and corrects collisions between machine components, in real-time, during post-processing. As a result, Virtual Machine® reduces scrap materials and minimizes tool replacements, while increasing machine utilization and improving part quality.
More Efficient Post & Model Development
The machine tool and controller data for both Virtual Machine and CAM-POST® are stored and managed in the same database. This eliminates the error-prone and time-consuming alternative of entering the same data twice when using a non-integrated solution.
Machine Tool Motion Simulation
Virtual Machine® may be synchronized with the CAM-POST® interface at any collision or over-travel error; thereby, allowing the user to graphically examine the part program and tape output precisely where the problem occurred. With this powerful tool, errors that could have damaged the part, tool and fixture can be eliminated.
Complete Integration with CAM-POST® & More
Get even more efficient NC Code in less time by adopting the unique Adaptive Post-Processing technology. By running CNC simulation, tool-path optimization and post-process in one process, you can save 25% to 35% in programming and machining cycle time.

Post-Processor Development
The CAM-POST platform is an advanced CNC post-processor builder that supports multi-axis machines and all major CAD/CAM Systems. Its flexibility allows it to generate efficient GCode for all CNC Machine-Controller pairs.

Custom Post-Processors
Looking to have a post-processor built for your machine? ICAM’s dedicated post-processors for CATIA, Mastercam, NX CAM & more are trusted by industry leaders worldwide to deliver substantial cost savings.

Tool-Path Optimization
ICAM’s SmartPACK optimizes your NC Code by finding the most efficient path between two points, eliminating time-wasting air-cuts and providing automatic feed-rate adjustment based on changes in depth-of-cut.
A CNC Simulator with Real-World Savings
Virtual Machine® is designed from the gate to deliver substantial savings in NC programming time. By testing while you develop your post-processor, you can considerably cut down on the time you spend testing, modifying and retesting your CAM code.
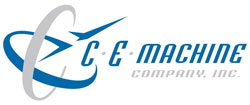
” Before we purchased ICAM, programmers at C.E. Machine had to generate NCI through the CAM software, use a third party post-processing software to post, and then import all part, stock, and tool models into a separate verification software before programs could be sent to the shop floor. With the solution ICAM has provided, programmers now use a single software suite to do all of the above simultaneously. “
Aaron Schwaiger, NC Programmer at C.E. Machine Company
Get a Free Demonstration of how CAM-POST Integrates into your existing setup.
No matter your specific manufacturing needs and constraints ICAM’s team of dedicated Post-Processor engineers can provide the ideal solution for your situation. They will take the time to understand and evaluate your existing process in order to deliver the most powerful and refined post-processing solution possible.
Get in touch today and a member of our team will get back to you shortly.